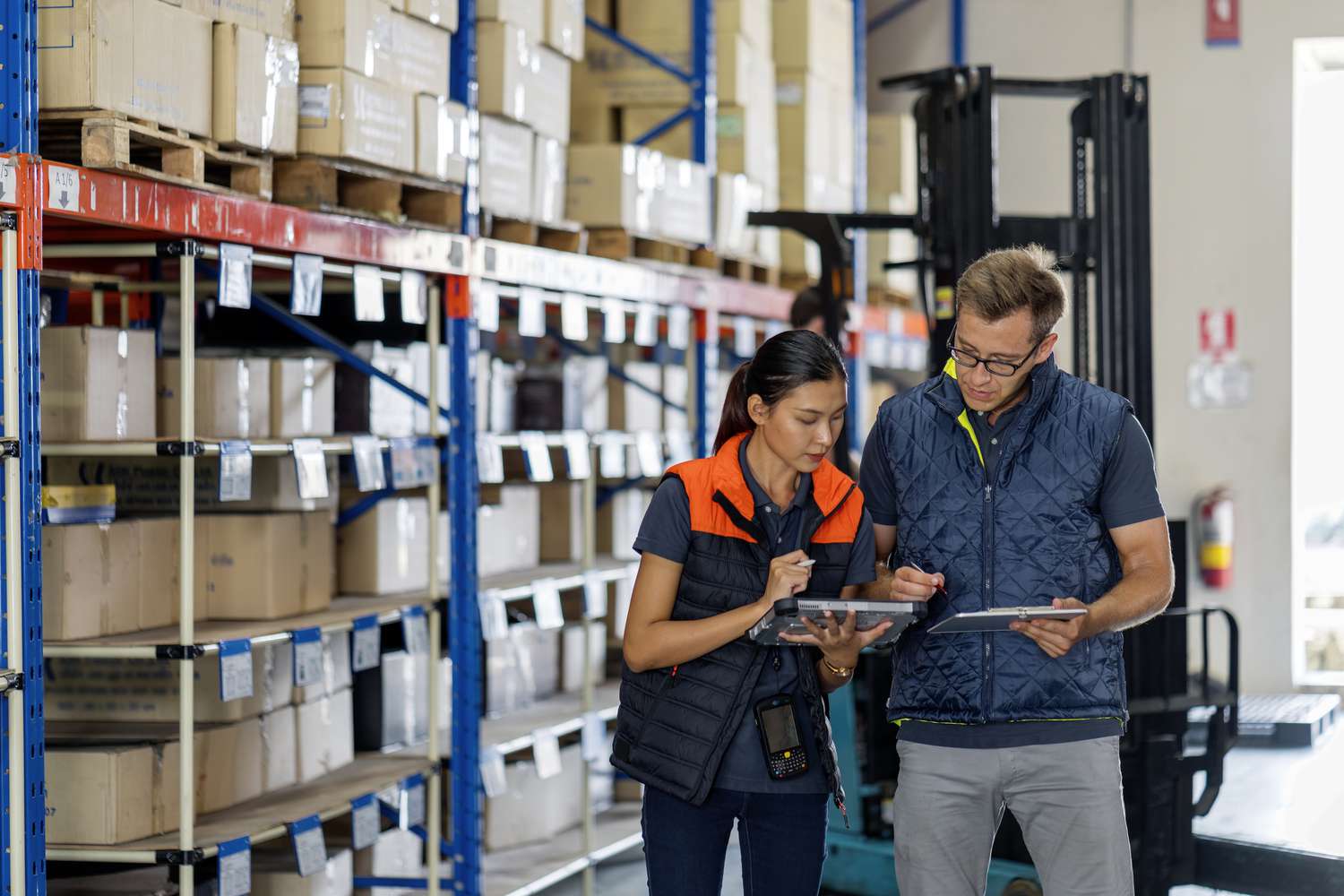
Mastering Purchasing and Inventory Management: A Comprehensive Guide
Purchasing and inventory management form the backbone of any successful business, influencing everything from customer satisfaction to cost control. In this comprehensive guide, we’ll dive into the intricacies of these critical processes, uncovering strategies to optimize them for maximum efficiency and profitability.
Understanding Purchasing and Inventory Management
Purchasing and inventory management are interdependent functions that play a pivotal role in maintaining a healthy supply chain. Purchasing involves procuring the necessary materials, goods, and services to keep operations running smoothly, while inventory management focuses on maintaining optimal stock levels to meet customer demands. The primary objectives include minimizing costs, mitigating risks, and ensuring timely fulfillment of orders.
Types of Inventory
Various types of inventory exist within businesses, each serving a unique purpose. Raw materials are the building blocks of production, work-in-progress captures partially completed products, and finished goods are ready for sale. Additionally, MRO inventory facilitates day-to-day operations. Safety stock, anticipation inventory, and buffer stock act as safeguards against unexpected demand fluctuations, preventing stockouts and maintaining customer satisfaction.
Inventory Management Methods
Several inventory management methods offer distinct advantages depending on business needs. Just-in-Time (JIT) reduces waste by delivering materials exactly when needed, Economic Order Quantity (EOQ) minimizes ordering and holding costs, and ABC analysis categorizes items based on value and impact. Successful companies tailor these methods to their operations, achieving efficient inventory turnover and optimized supply chain performance.
Purchasing Process
The purchasing process involves a series of interconnected steps, from identifying procurement needs to order placement and beyond. Selecting reliable suppliers, building strong vendor relationships, and conducting thorough supplier evaluations contribute to successful procurement. Effective negotiation skills aid in securing favorable terms and pricing, resulting in cost savings and improved margins.
Technology in Inventory Management
Modern technology has revolutionized inventory management. Advanced inventory management software offers real-time tracking, automated reordering, and data-driven insights. RFID technology enhances visibility, enabling businesses to monitor inventory movement and optimize warehouse layouts. Implementing these technological tools not only streamlines operations but also improves accuracy and reduces manual errors.
Demand Forecasting
Accurate demand forecasting is essential for maintaining optimal inventory levels. Businesses utilize both qualitative and quantitative methods, leveraging data analysis, historical data, and market trends to predict future demand. By fine-tuning forecasting accuracy, companies can minimize overstocking and stockouts, enhancing customer satisfaction and reducing holding costs.
Inventory Auditing and Control
Regular inventory audits are vital for ensuring accurate inventory records. Audits help identify discrepancies and variances, which could arise due to theft, data entry errors, or other factors. Employing proper inventory control mechanisms, such as cycle counting and barcode scanning, aids in maintaining inventory accuracy and preventing costly issues down the line.
Challenges and Solutions
Inventory management isn’t without its challenges. Stockouts can lead to lost sales, while overstocking ties up valuable resources. Demand volatility and supply chain disruptions further complicate matters. Implementing safety stock, fostering collaborative relationships with suppliers, and adopting agile inventory management practices help businesses mitigate these challenges effectively.
Sustainable Inventory Practices
In today’s environmentally conscious landscape, sustainable inventory practices are gaining prominence. Reducing waste, optimizing transportation routes, and minimizing carbon emissions contribute not only to ecological responsibility but also to cost savings. Adopting sustainable practices enhances a company’s reputation and aligns with evolving consumer preferences.
Case Studies
Examining real-world case studies showcases how various companies have tackled purchasing and inventory management challenges. Companies like Toyota (JIT implementation) and Amazon (advanced technology integration) have leveraged innovative strategies to streamline their operations, enhance customer experiences, and drive profitability.
Takeaway
Purchasing and inventory management are dynamic processes that demand continuous improvement and adaptation. By understanding the intricacies of different inventory types, implementing effective management methods, embracing technology, and addressing challenges proactively, businesses can master these critical functions, ensuring sustained success in a competitive market.